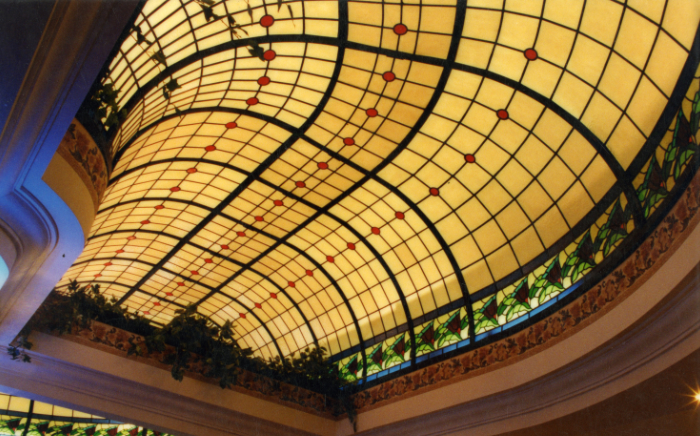
Producing glass perfection for super-rich clients
Daedalian Glass Studios creates large-scale, decorative glass installations, using an array of glass techniques, primarily for the super-prime residential, five-star hospitality, and superyacht sectors. Established in 1986 by Davia Walmsley, the business is now run by her son, Joe Walmsley. Find out more about this studio, which handles everything from design to installation for its exacting clients, in this interview with Joe.
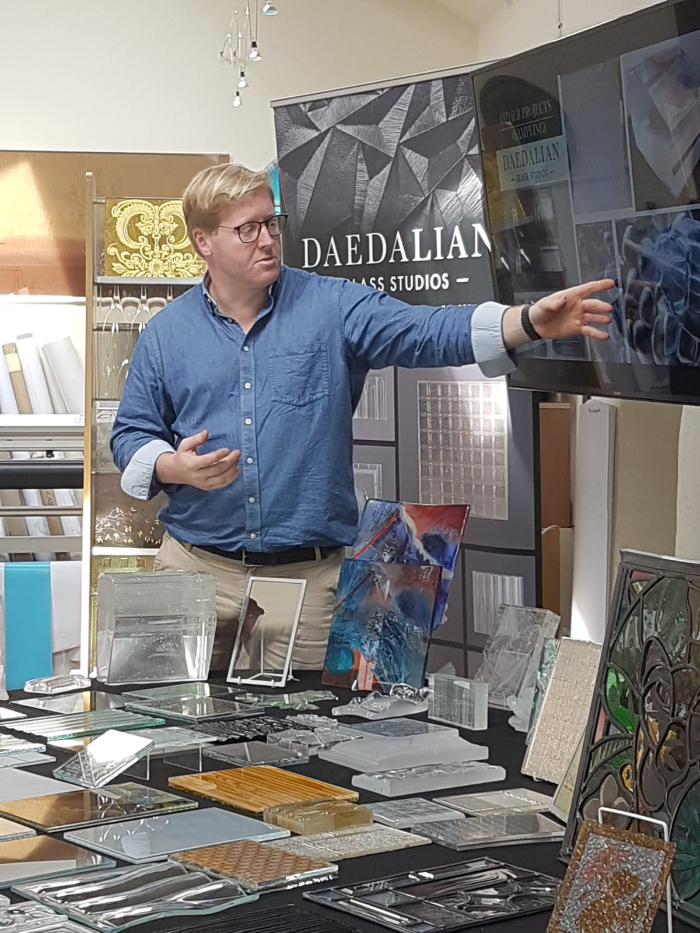
You almost grew up in the glass studio. What is the first project you remember working on and what tasks did you help with in those early days?
There was a project for a bar called ‘Lawdy, Miss Clawdy’ (named after the Elvis Presley song) in our local town, Poulton-Le-Fylde, that I first helped with in the 1990s. It was a huge, torus-shaped skylight, like an elongated circle, made from leaded lights with integrated steel bars for structural stability (see main feature image). The studios were (and are) next door to my parents’ house, so in my teens I would go to see them after school. This commission was a large project for the studios at that point, so my mum would not always finish at 5pm. I would help her by passing her tools and the sheets of glass she needed, then later I helped with the finishing – the blacking polish and cleaning the glass.
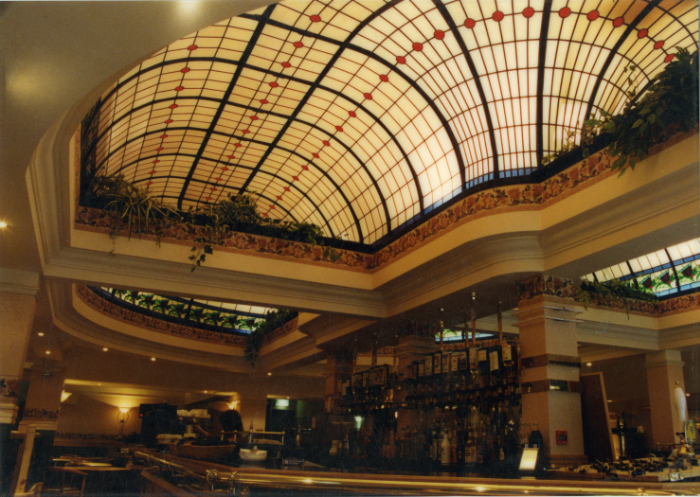
Your time is mainly taken up by the operations side of the business these days, but you occasionally help in the glass studio. What’s your favourite glass working technique?
It must be kiln cast lead-crystal glass. It is such a versatile process that can bring very intricate and ornate concepts into reality. We have had some amazing cast glass commissions in the past few years – custom wall lights, decorative inlaid marquetry panels, floor-to-ceiling decorative glazing, and cast architectural mouldings, like skirting boards, dado rails, sconces, and even entire fireplaces!
Unfortunately I cannot say too much about many of these projects as most of our casting work is bespoke, one-off pieces under strict non-disclosure agreements (NDAs). If CGS members wish to see these pieces, though, we are currently advertising for a studio technician job!
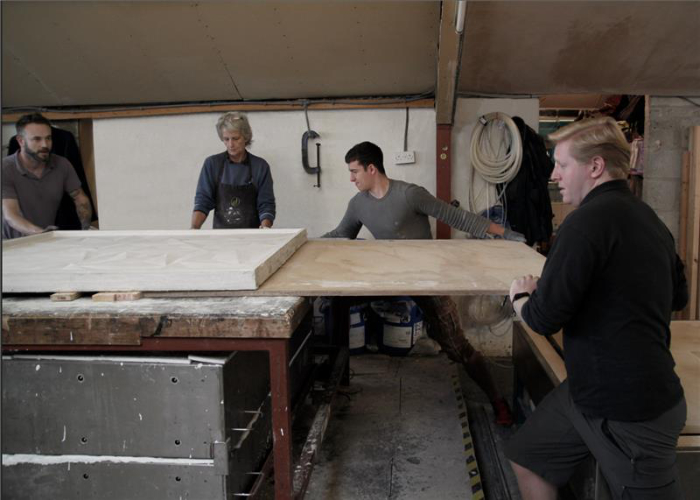
Between 2006 and 2012 you went to work in corporate finance in the City of London. What lessons from this experience have you applied to the running of a glass studio?
Of course, working in the City provided me with a strong understanding of how to structure the business financially, in a way that will best facilitate the continuation of its natural growth ark.
In the past five years we have implemented a significant investment programme in the studio facilities. We built a whole new studio area that expanded our space, part of which was used to house a new, automated sandblasting machine. Before this we only had a hand-held sandblaster. We still use this to achieve very fine, intricate details. However, the automated sandblaster allows us to put a flat, even sandblast across panels, without having to have a skilled technician there. It also allows us to do a gradient sandblast across panels, which is almost impossible to do by hand.
Next, we invested in a purpose-built sandblasting/gilding studio. Prior to this we had to outsource some of our silvering, which was problematic, in terms of the extra time required for the process, managing the quality control, and managing project costs.
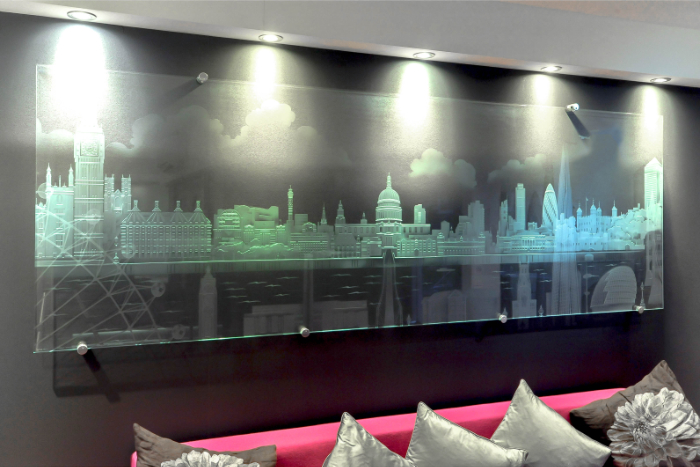
Since your return, and subsequently taking on the Managing Director role in 2017, what do you consider to be your greatest achievement?
Well, I have just mentioned the investment programme. These investments have given Daedalian Glass Studios the machinery and space to continue growth. This growth is not a new trajectory for the studios though; it was happening under the guidance of my parents, Davia and Chris, for over 30 years before I took over as MD. Davia managed the studio side and Chris managed the installations and office side. They still offer their assistance in these departments, and I would say my greatest achievement as MD is to continue their legacy and hard work.
Do you have any future investment plans?
There are always future plans! If you don’t keep moving forward, you stagnate. Our unique selling point is that we offer such a range of glass working techniques on-site. One of the few things we don’t have is a furnace to work with hot glass. It is also the area of glass working my mum first did. She had a job with the Venetian glass blowers prior to founding her own studio; this is actually the job that brought her to live in the North-West. I would like us to offer glass blowing and also hot pour casting.
How do you maintain quality control in an industry dominated by terms such as ‘industry standard deviations and allowances’?
You just need to be clear from the outset when sourcing raw materials. We explain who we are and the level of quality that our clients require. If they cannot match that quality then we source a supplier who can. If this is not available, we look to bring the process in house.
For things like float glass panels, obviously we cannot feasibly bring a glass production plant in-house. However, if the industry standard is to accept some minor surface level scratches, then we can hand-polish the glass to remove these. It is time consuming, but it is important to maintain standards.
Your main focus, and biggest commissions, are in the super-prime residential sector. Do you see more new markets opening up in the future, and what does the future hold for Daedalian?
Daedalian Glass Studios has changed the primary market it serves a number of times during its history. Originally it was an outlet for Davia to sell her private commissions. Then, in the early growth years, the majority of work came from commissions in the pub trade, such as traditional style windows and partition screens in etched and stained glass. There was also a period of focus on ecclesiastical work. Nowadays, the focus is on the super-prime residential sector.
In recent years we have been gathering momentum in the superyacht industry. We have done some interesting projects in that area. Again, these projects are almost always bound by NDA’s so we cannot feature them on our website.
Looking more long-term, we are already at the advent of automated cars and this offers interesting opportunities. In theory, should all vehicles on the road become automated, there should be no crashes. Then materials such as glass, which are highly regulated at present because of safety issues, would become less regulated. This would open up the bespoke car interiors market to companies like ours. There are already some concept cars touching on this in their interiors.
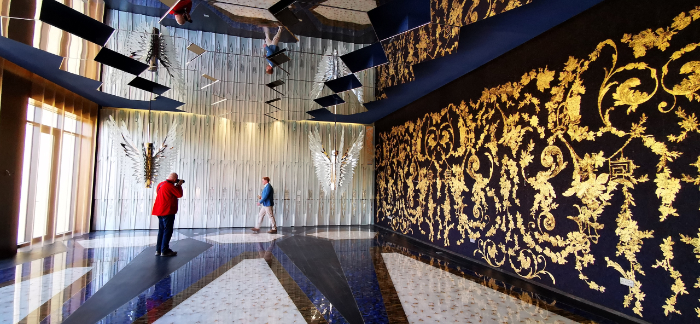
It has been an unstable few years. First Brexit, then the coronavirus, and now the war in Ukraine. How have these events affected the studios?
We were lucky when COVID-19 first emerged as we were already in the process of moving all our IT over to cloud-based systems. This switch was instigated to allow our teams, such as the business development and installations people, to access our servers when meeting clients or on-site, and it allowed all our office staff to work from home during the pandemic.
Another bit of good fortune was that we had a large project ongoing in London when the first lockdown began. As active construction sites were exempt under certain conditions, and we were providing the external glazing to secure the building, we were allowed to keep a limited team active.
Over the past few years, for whatever reason, we have seen volatile markets. At times, we have had to increase deposit payments to secure orders for raw material imports. This ensures we get them at the cost we have allowed for in the quote, rather than gambling.
With the war in Ukraine, and sanctions against Russia and its citizens, we have had a few projects either put on hold or cancelled completely, both from Russian and Ukrainian clients. We have been so busy in the studio recently, though, so we have easily filled any gaps in the production schedule.
Finally, what has been your favourite Daedalian Glass Studios project?
We worked on a project in Highgate, North London, where the brief was to create a series of bespoke, cast lead crystal lights atop Corinthian column capitals to sit around a subterranean swimming pool. They were interesting as they were clad around existing structural columns and needed to be designed in such a way that they could be safely deconstructed to change a lightbulb.
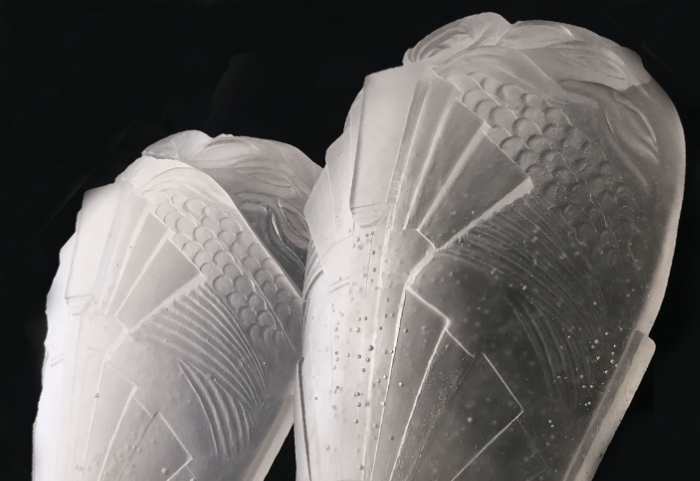
It was the first project we did that used 3D printing to mock up the exact shapes required. Also, the Chihuly Studio created work for the same area. It is a massive compliment to see our work commissioned and placed alongside other artists we greatly respect, such as that of Dale Chihuly.
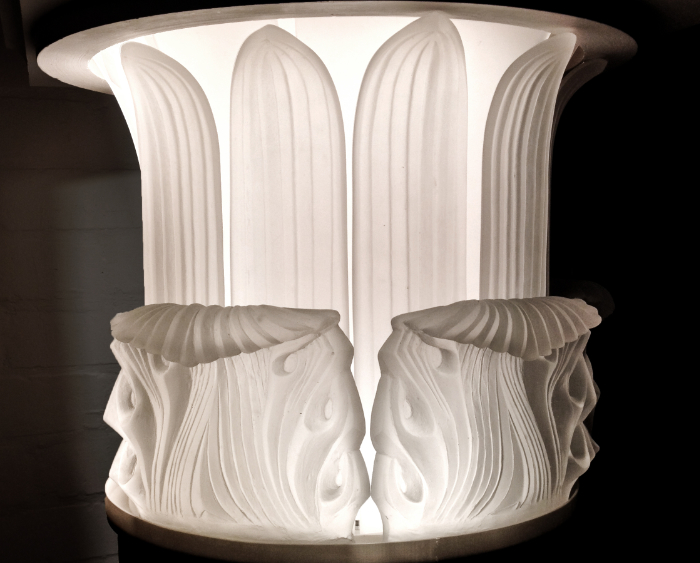
More about Daedalian Glass Studios
The Daedalian Glass Studios provides a wide array of glass working techniques, providing large-scale glass commissions, and a full-service offering, comprising design, glass studio and installations teams.
Glass working techniques include:
- Etched glass – automated and hand-held sandblasting, as well as hand-drilled glass
- Stained glass and leaded lights
- Laminated glass – including interlayers, such as fabrics, metal mesh, wood and stone veneers, leaf skeletons, paper, and digital films.
- Silvered and gilded glass – metal leaf, spray silvered, verre églomisé, hand antiqued
- Back-painted glass
- Warm glass – kiln formed, kiln slumped, kiln fused (tack and full fusing), and kiln cast.
Managing Director Joe Walmsley focuses on the operational side of the business, but lends his talents to help the glass studios, conduct site surveys, or work with the installations team.
Visit the Daedalian Glass Studios website here.
Main feature image: Joe first helped out on a large skylight project for a bar called ‘Lawdy, Miss Clawdy’.